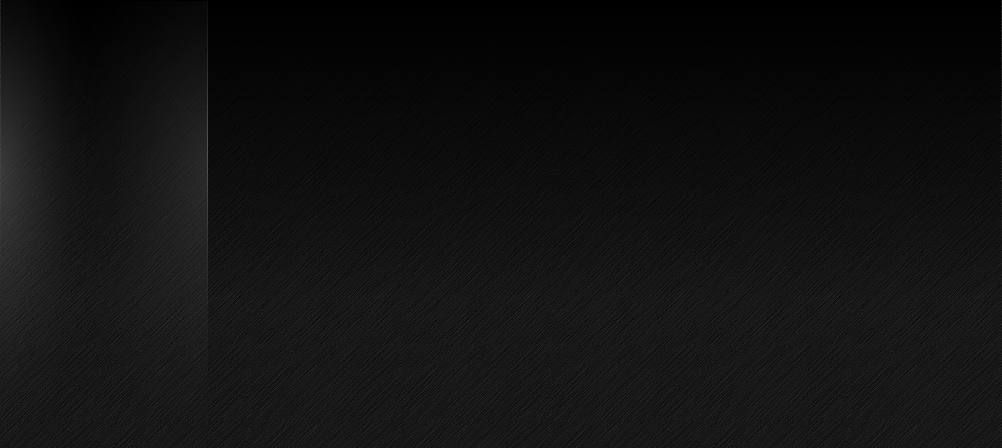
Tel:020-8469-2580
Fax:the 020-8469-2589
E-mail: 13928725580 @139.com
Address: FL. 1, BLOCK 7, No.2 INDUSTRY AREA OF SHAXU, KENGKOU ROAD, SHIQIAO TOWN, PANYU DISTRICT,GUANGZHOU, CHINA
The difference between Digital Wax Injector and ordinary wax injector
1.High precision of the temperature
As ordinary wax injector adopts the simulating logic circuits, the temperature control system changes with the length of the usage time. After service for two or three years, the temperature of the wax injector may deviate for 3℃ or even 10℃.
However, the Digital Wax Injector adopts the digital circuits which would never alter with the length of the service time. Therefore, it would prevent the generation of the bubbles and thus effectively control the weight of the wax mould.
2.High precision of the injecting time
As ordinary wax injector adopts the simulating logic circuits, the temperature control system changes with the length of the usage time. After service for two or three years, the injecting time may deviate for around 0.5 seconds.
However, the Digital Wax Injector adopts the digital circuits, and the CPU timing controller it uses would not alter with the length of the usage time, thus can effectively control the weight of the wax mould.
3.The unique functions of the Digital Wax Injector
To use the program to set the functions such as fixed-time starts and automatically wax boiling (reducing the generation of the bubbles during the process of melting the wax).
Market requirements:
As gold and silver prices kept rising these 2 to 3 years, coupled with the exponentially increase of domestic labor as well as the price rise of the basic raw materials such as oil and natural gas, the profits of jewelry industry certainly reduce greatly. Orders from Europe and America shrink significantly, and processing fee of factories keeps dropping. Under such circumstance, business owners could only squeeze out profits in the production process to survive.
Idea one: reduce the gold and silver losses during the production process----increase equipments to improve the recovery rates and reduce the losses.
Idea two: lower the labor cost by reducing the number of workers----increase equipments to improve the production efficiency and reduce the workers overhead.
Where shall we start from? I think controlling the sector of casting is the most direct and effective way. Increasing equipments such as furnace and casting machines helps to reduce the wastage and the labor cost, strictly control the gold and silver losses rate, sharply improve the casting quality, and thus ensures the high efficiency and low wastage rate of the follow-up processes of filing and polishing, leading to the decrease of the workers in these processes or even the adoption of machinery polishing devices.
The initial investment of the traditional vacuum casting device is considerably low, namely, around 10,000 to 30,000 RMB for whole set of equipment, thus it’s easy to get started. Using the melting equipment would need at least 50,000 to 60,000 RMB, or even 500,000 to 600,000 RMB. Even the cheapest melting furnace on the market costs 7,000 to 8,000 RMB. The melting furnace may reduce the gold and silver losses yet the operation cost is not low: large power consumption and high failure rate, which directly affect the production cycle. Some of them may cause higher gold and silver losses due to the unstable heating capacity. All these have scared away the business owners.
Features:
1.Security and stability-----the heating system adopts Japanese technology, with over 20 years stability and reliability confirmation.
2.Great energy efficiency-----advanced electronic control circuit and special chassis structures make its thermal energy conversion rate 30-40% higher than similar products and would reduce electricity consumption by over 30%.
3.Quality uniform-----stable electronic control circuit and optimized PID temperature control ensure the stabile quality of the casting, and with a higher quality reproduction capacity compare with traditional vacuum casting technology.(torch)
4.Ultra-low loss-----the visibility of the PID temperature control realizes the stability of the casting temperature and the great reduction of the material melting loss. The melting loss of traditional vacuum casting technology (ignition lance) is approximately 0.1-0.5%,while that of melting furnace is around 0.02-0.05% and can be easily recycled, thus the loss of the latter is almost negligible.
5.Environment improvement-----the working environment of the traditional vacuum casting technology (ignition lance) is extremely bad: in summer it makes the indoor temperature up to 40-50℃ and the noise up to 80 decibels plus; moreover, the glaring flames make the workers suffering a lot, and the usage of flammable and explosive gases such as acetylene and oxygen worry the business owner very much. And will never be complained by the neighbors.